An unexpected moment of surprise on the approach to the Fronius plant site in Sattledt, Upper Austria: is the characteristic horse-head pump in the immediate vicinity of the access road, whose balancer continuously moves up and down, really used for oil production? "Yes, we are actually sitting on an oil field here, but we have nothing to do with the pump in front of our plant," smiles Martin Hackl, who has been responsible for Fronius' international solar business for years. "All the more important that we show that there is another way," he adds enthusiastically.
This starts with the inverter manufacturer's own energy supply. Since February 2023, all Fronius production sites in Austria have been operated entirely without fossil fuels. Sattledt is at the forefront of this.
Factory completely converted to electricity
The factory has been completely electrified. Even the heat for the electroplating processes is supplied by electric heating rods - powered by the solar modules on the roofs of the production halls. These achieve an output of 2.235 megawatts and can partly supply the factory with solar power. The rest comes from the grid in the form of certified green electricity.
The roof terrace offers an impressive panorama of the new, architecturally appealing production hall. Thousands of solar modules are mounted in rows of two on the divided, brown building axes, with atriums in between and green ramps to the outside. Well hidden in the ground is a special highlight. Two ice storage units, which heat Fronius' largest production site in winter with an output of eight megawatts and cool it in summer with an output of 6.3 megawatts.
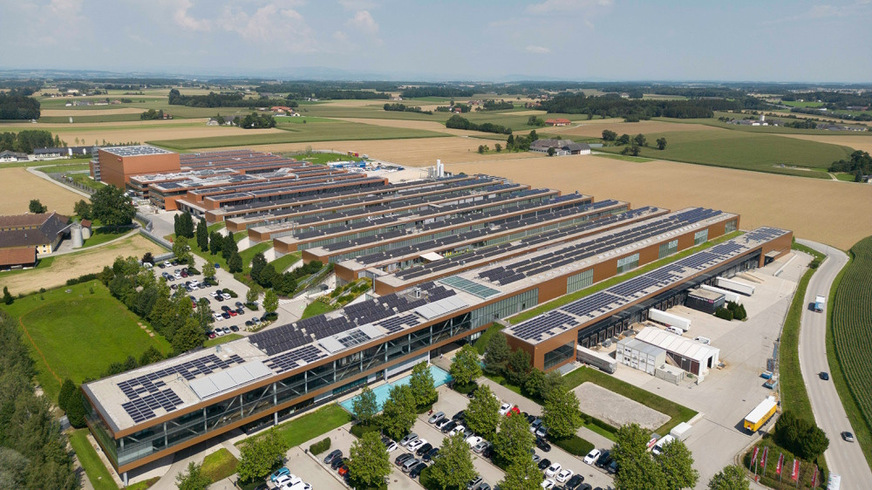
Fronius International
52,000 devices per month
By commissioning the new production hall, Fronius has significantly expanded its production capacity. This year, the company will be able to produce 52,000 inverters per month. By comparison, 32,000 inverters rolled off the production line every month in 2022. This brings the total annual production capacity to seven gigawatts, compared to four gigawatts last year. The family-run company invested 187 million euros in the expansion and modernization of production in Sattledt last year and another 230 million euros this year.
Partially automated production
Partial automation, an innovative logistics concept and quality assurance play an important role. A fully automated high-bay warehouse offers space for 7,000 pallets and 12,500 small parts containers. The production lines are supplied with pre-picked component packages via conveyor belts and driverless transporters. Final tests and an endurance test are carried out automatically in the modernized test center.
Successfully tested devices are transported on to the dispatch area. Storage and retrieval in the new high-bay warehouse is also fully automated. Outgoing goods capacities have been doubled.
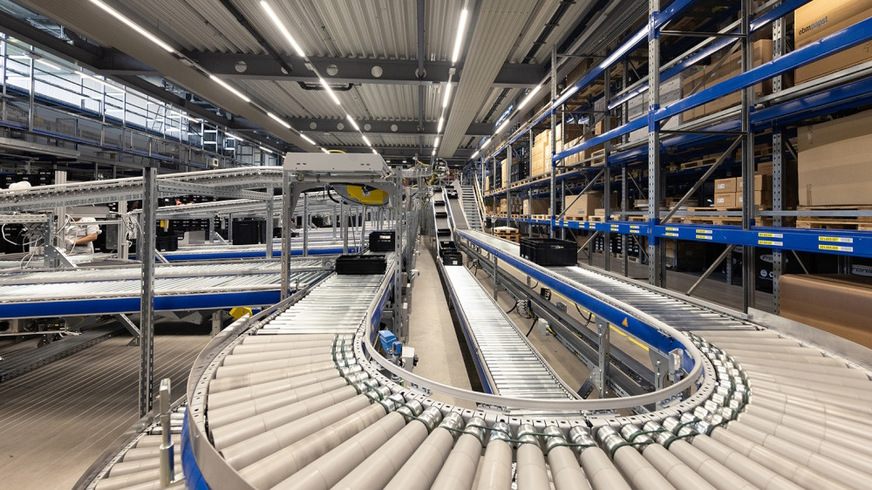
Fronius International
Attracting employees
However, despite all the modern technology, it ultimately comes down to the employees, as Thomas Herndler, Chief Operating Officer at Fronius International, emphasizes. This is why employee development is so important. For example, new, flexible working time models are offered for shift work and new lighting technology is installed that is based on the natural course of daylight (so-called human-centric lighting) to enable shift workers in particular to sleep better.
Two social coaches have been hired to act as contact persons for private problems. In order to attract new specialists, the company is also focusing on a broad-based recruiting campaign, benefiting from its strong roots in the region, reports Martin Hackl.
Further expansion already planned
Fronius is also increasingly recruiting specialists via its current 26 international locations. The company currently has a total of around 8,000 employees worldwide. Fronius has taken on over 1,700 new employees since last year, 1,000 this year alone.
The signs are pointing to further growth. Fronius is aiming to expand its monthly production capacity to 70,000 inverters by 2024, with an annual output of 10.5 gigawatts. The company also intends to achieve this growth through a new contract manufacturing facility in Hungary. Fronius has also set up its own research and development department at its US site in Portage, Indiana, in order to develop products for the American market. There are also plans to set up production lines there in the future.
81,000 installers in the network
The company will open new branches in Belgium, Portugal and Romania, among other countries. "Internationalization has enabled our strong growth in the past and will continue to strengthen us as a European manufacturer in the future," says Elisabeth Engelbrechtsmüller Strauß, Managing Director of Fronius International.
The global partner and installer network is also to be further expanded. According to Hackl, the company currently works with 81,000 installers, 14,000 of which have been added in the last twelve months. Worldwide, 4,000 installers are Fronius system partners.
Did you miss our video? Leonhard Peböck and Robert Müllehner from Fronius: Sector coupling all from one hand
The global company also offers a 24-hour after-sales service across all time zones. Pure production capacity is only one aspect of Fronius' strategy for further growth. The inverters produced must also be sold - as a European manufacturer against competitors from the Far East, this is no longer an easy task.
Digital support for repairs
This is why Fronius has long been focusing on added value for installers and system operators. This ranges from the most efficient possible control of energy flows to service offerings for tradespeople, such as the Fronius Solar SOS digital platform.
This supports the installer in the after-sales service when analyzing the fault of a defective inverter. By entering the serial number, an error description or the error code, they receive digital support to identify the error and repair the device. "Only if they cannot solve the problem in this way do they call our service center. The process is then already registered in the system and our service technician already has all the information. This enables them to provide very quick support in rectifying the fault," says Hackl.
More than just replacing circuit boards
The partner installers are specially trained for the repair and have a case with the appropriate spare parts. If the right spare part is missing, the technician can order it directly via the SOS platform. Fronius goes beyond simply replacing circuit boards. The sustainability concept goes much further.
On the one hand, the defective components are sent to a Fronius repair center and - if possible - reconditioned there. In addition to replacing individual components of the inverter, there is also the option of replacing the entire device.
Repairability as a strategy
Fronius has built up a stock of refurbished inverters of all generations for this purpose. "We send such a suitable device to the installer. They replace it with the defective inverter and send it to one of our repair centers. There, our technicians recondition the defective inverter and add it to the stock of replacement devices," explains Hackl.
Such a concept cannot be implemented overnight. This is because repairability must be taken into account as early as the product development stage. "A repairable inverter must be designed differently. The components must be installed and integrated in such a way that they are easy to replace. In addition, the installers must be appropriately trained and educated so that they can also carry out the repair," says Martin Hackl. "We have strategically developed this concept over two decades and it is the benchmark for sustainability in the aftersales sector."
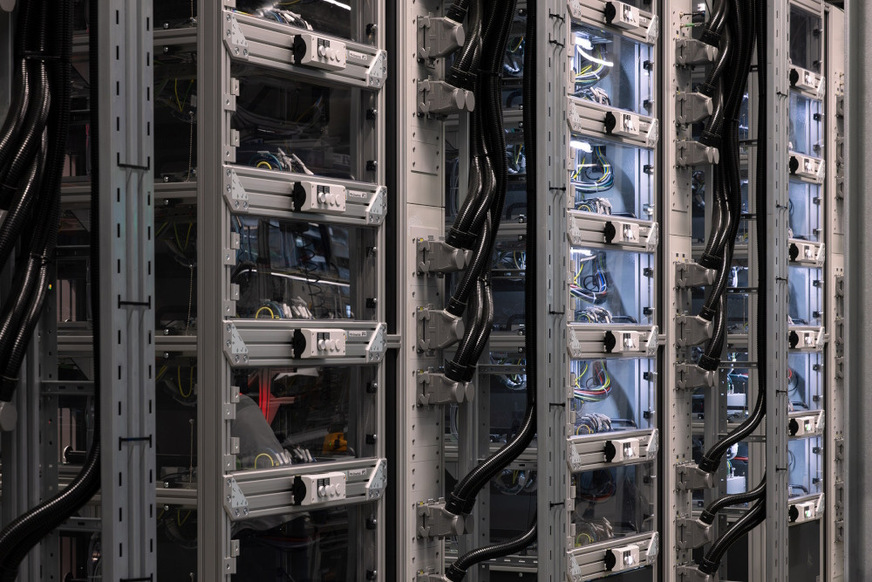
Fronius International
Reconditioning components
But Fronius is now going even further. In the next step, the company wants to design the inverters in such a way that the materials used are recycled. The basic idea is to design the devices like a modular system. This means that in future, component groups - both new and refurbished - from older generations of devices can be reused in new inverters.
The next generation of inverters will therefore be closely based on the current Fronius series. "Ideally, we will be able to reuse heat sinks, for example, that are installed in a current GEN24 inverter in the future generation. This reduces the carbon footprint immensely, especially with aluminum parts like these," says Martin Hackl.
Starting the material cycle
Fronius can draw on the experience gained from repairs. For example, there is an aluminum washing system at the Raparaturzentrum in Steinhaus near Wels. The dismantled heat sinks are cleaned there and are then as good as new. "We want to achieve this with several components. Ideally, this will bring us into a material cycle. We then want to adapt this in the development of new products," emphasizes Hackl.
Of course, Fronius cannot do without using the latest generations of processors. But reuse is certainly possible for many components.
That sounds like a lot of work. But for Fronius, it is the way to position itself on the market as a European manufacturer. The company does not want to wait for any kind of European industrial policy. This positioning also includes concentrating on segments where Fronius can play to its strengths: self-consumption in residential and small and medium-sized commercial buildings.
Also interesting: Fronius takes the complete life cycle of the solar system into account
This distinguishes the European production of power electronics from module production in Europe. There is intelligence in the inverter. It is about controlling entire energy flows and not just converting direct current into alternating current.
Keeping an eye on the price gap
Fronius has also built up this expertise over many years with its products for sector coupling such as Ohm and Wattpilot. "This gives us the feeling that we are competitive with the way we work," says Martin Hackl. "Of course, this is becoming more and more challenging because we still have to make sure that the price gap doesn't widen too far."
This strategy has been well received by the installers. Production is well booked and there were even supply bottlenecks last year. This is because the supply chains for raw materials were interrupted. This also affected Fronius, a company that manufactures some of its own components.
However, this high degree of vertical integration has not prevented Fronius from being dependent on fragile supply chains. They have now stabilized. Fronius has also changed the structure of its suppliers. "We now have an even closer relationship with our suppliers than before," explains Martin Hackl. "This may make us a little less flexible. But it makes a difference whether you are given preferential or normal delivery."
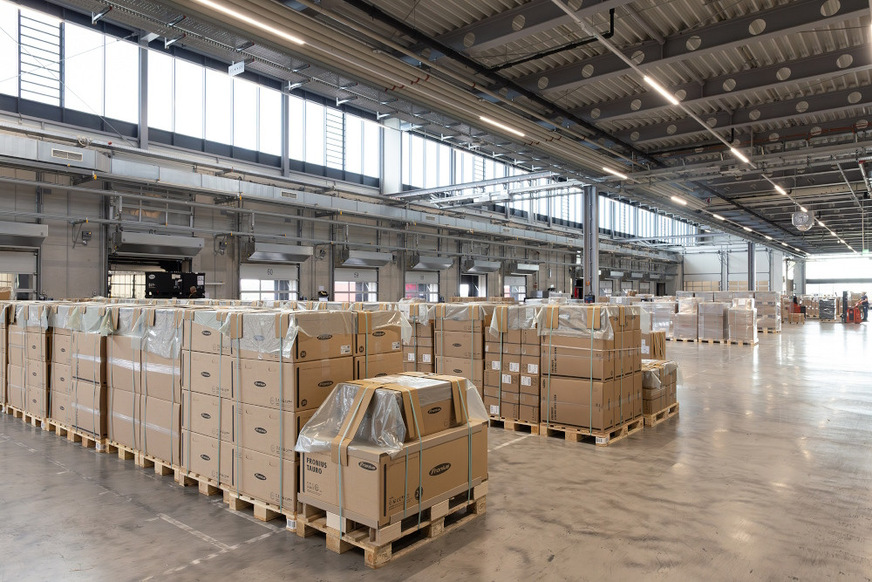
Fronius International
Devices are available again
These partnerships primarily concern key components for electronics, i.e. circuit boards, coils and capacitors, "so that we are well supplied in the long term." This has an impact on the ability to supply inverters, which has been restored for all products. The inverters are once again available within normal delivery times. "We still have full order books. But we are now producing in such a way that the market can be supplied as normal," says Hackl. This means that wholesalers have stocks and can deliver immediately. (Hans-Christoph Neidlein/Sven Ullrich)
Read our interview with Martin Hackl, Director of the Solar Division at Fronius International, about product innovations.