The station forecourt in Freiberg am Neckar (Baden-Württemberg/Germany), which has a population of 16,000, looks tranquil on this sunny late fall morning. Just under five minutes away by electric car, directly behind the A8 freeway underpass, the headquarters of the mechanical and plant engineering company Teamtechnik beats with a dynamic pulse of the future. A good 550 employees develop and produce high-tech automation solutions for the e-mobility, medical technology and new energy (PV and battery technology) sectors in buildings that are partly futuristic in style.
Among other things, the company is a technology leader in the development of production systems for the manufacturing of solar cell strings for photovoltaic modules. Teamtechnik employs 1,100 people worldwide at 7 production and 13 service locations. Since 2021, Teamtechnik has been part of the Dürr Group (18,000 employees), which has just completed the acquisition of another automation company, BBS Automation. Within the Group, BBS and Teamtechnik form the "Production Automation Systems" division with a combined turnover of around € 500 million.
Active in the solar sector since 2004
Teamtechnik entered the solar technology market back in 2004. In 2006, the first generation of high-performance stringers for the production of solar cell strings was presented at leading international trade fairs. This was followed in 2010 by the construction of a new 2,300 m2 production hall for the solar sector in Freiberg. One stringer system was delivered every week. In the same year, the Swabian mechanical engineering company also made the move into China with the founding of Teamtechnik Production Technology Ltd. in Jintan and Suzhou.
By 2012, the company had already sold a production capacity of several GWp of solar stringers, making it the global market leader in this field. The photovoltaic business boomed and this was followed by further major orders from China. In the last quarter of 2013 alone, the large Chinese solar module factories ordered over 50 stringer systems from Teamtechnik. "A cell in 2.25 seconds" was the slogan in 2014, when the Swabians presented the world's fastest stringer system in China at the time.
Bonding instead of soldering for high-efficiency solar cells
And the innovation spiral continues. The current cycle time is 0.85 seconds for the TT4200 i8 and 0.9 seconds for the TT4000 i8 ECA. The TT4200 i8 works with conventional IR light soldering and is mainly used in the production of solar cell strings with PERC or TopCon technology. The TT4000 i8 ECA was developed with a specially developed bonding process for connecting the latest generation of high-efficiency heterojunction (HJT) and multijunction (tandem solar cells) solar cells. Heterojunction and tandem solar cells combine conventional crystalline solar cells with a thin film of amorphous silicon or another semiconductor material, such as perovskite.
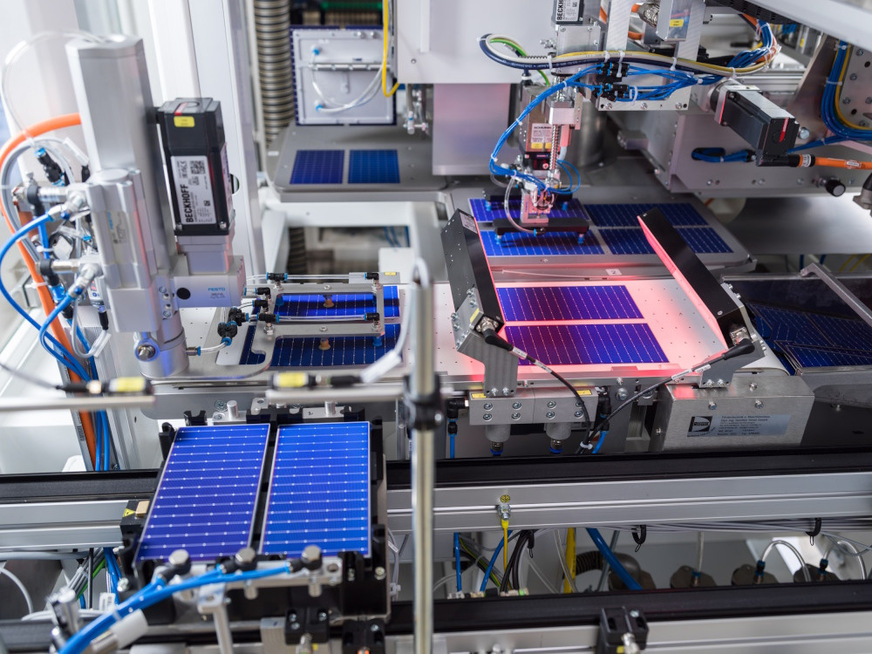
Teamtechnik
In the bonding process, an electrically conductive adhesive (ECA) is printed on both sides of the cells in a first step. In the second step, the metallic cell connectors are embedded in the adhesive and the cell connection is cured at a low temperature. This process is thermally and mechanically particularly gentle on the sensitive layers of modern solar cells, which are becoming ever thinner. It reduces the occurrence of so-called "microcracks" (minimal damage to the cell structure), is lead-free and allows the processing of so-called "busbarless" cells. "Dispensing with lead makes solar module production more environmentally friendly and recycling easier," says Teamtechnik spokesman Philipp Enzel, adding that the use of busbarless cells saves raw materials in cell production. At the end of October, the company was therefore nominated with the new technology for the final round of the Baden-Württemberg Environmental Technology Award in the "Material Efficiency" category.
"Bonding technology is currently still a niche market for stringers, but it is becoming increasingly important. This is because modern solar cells are not only becoming more powerful, but also thinner and more sensitive," says Michael Schäfer, Senior Account Manager Solar. The first orders in the gigawatt range have now been received.
Precision and speed are crucial
A number of the new, white stringers are lined up in the production hall, sparkling clean, and are checked again and approved by the customer before delivery. They are packed with automated precision tools, grippers with suction cups, roller conveyors, light barriers, cameras, other electronics, cables and hoses in a very small space. In a matter of seconds, the fine cell wires are glued or soldered onto the supplied raw cells and connected to form cell strings. "Precision and speed are crucial," emphasizes Enzel. The core competence in the development of the machines and automation solutions is the software, whereby Teamtechnik also works together with control specialists such as Beckhoff. A stringer of the new generation can connect solar cells with a total output of around 125 - 145 megawatts per year.
Teamtechnik experts also accompany the installation of the stringers in the PV factories on site, instruct the specialist personnel in their operation, offer training and take care of maintenance and, if necessary, subsequent updates and modernization of the production lines.
Export stringer business to China a thing of the past
However, the days when the Swabians sold their stringers in large quantities in China are over. "We can no longer sell stringers from Germany to China at the moment, and that won't happen again," says Schäfer. This is because the Chinese have greatly developed their own plant and mechanical engineering in recent years and now produce their own stringers for the major PV manufacturers in China. Meanwhile, Teamtechnik primarily manufactures systems for the e-mobility sector in China.
Did you miss that? Sustainability and more
Teamtechnik is now focusing all the more on PV production and a renaissance of high-performance solar cell production in Europe and the USA as a sales market. The first steps are now being taken, says Enzel. "But without a common European strategy, it will be difficult to rebuild PV production locally," emphasizes Enzel.
Also interesting: European PV industry against solar trade defence measures
„After all, China and the USA are currently massively subsidizing their own industries and distorting the markets. This is why the European solar module production market has not yet developed properly, as companies are currently investing in the USA rather than in Europe“, he says. However, know-how, inventiveness and pioneering spirit are also available in "good old Europe", as the example of Teamtechnik shows. (hcn)