You have already gained a lot of experience with BIPV. How has the industry changed and developed in recent years?
At the moment we are experiencing a real boom in photovoltaics in general. BIPV is also benefiting from this. Now that module manufacturers and facade builders are devoting more attention to this topic again, there is a real boom in BIPV compared to the past. In addition to the fact that solar energy is currently in greater demand, this is also due to all the building regulations and solar obligations for buildings, especially in Switzerland, but also in Austria and Germany.
So BIPV is on its way out of the niche?
It is developing well, and we now have to see whether the current wave will subside again. Because planners are still partly overwhelmed and urgently need information. Of course, there is now plenty of information on websites that deal with BIPV, and advisory services such as that of the BAIP from the Helmholtz Centre Berlin or other contact points also offer sound initial information. But there is still the question of whether architects and planners will face up to the effort and bring photovoltaics into the building envelope.
But we already have to use the potential to achieve the expansion targets, don't we?
Yes, we do. But it is not necessary to implement any extremely complicated BIPV projects, such as on historical buildings or the like. Because there are many other buildings available. And I believe that there is still huge potential in renovating the existing stock. Certainly, it's more complicated than in new construction. But if you look in Switzerland, there are also lots of projects where BIPV has been implemented in existing buildings.
You are actively approaching architects with your new company Arconsol. How do they react when you confront them with BIPV?
That has changed completely compared to the past. Now they are much more open, because they are not only confronted with the new regulations, but also because of customer requirements and are urgently looking for solutions.
What questions then come up again and again in the discussions?
In addition to questions about design possibilities, economic efficiency and the smooth handling of BIPV projects, fire protection is currently a hot topic, especially in Germany. The question here is how BIPV modules can meet the fire protection requirements in tall buildings. After all, above a certain height, fire loads are no longer allowed in high-rise buildings. There, the solar modules must then achieve fire protection class A2 or A1, i.e. they must no longer be combustible.
Where is the challenge here and what could a solution look like?
The fire load is mainly in the foil in which the solar cells are embedded. Here it can be helpful to test and certify entire systems, i.e. the module together with a mounting structure. It would be quite possible to insert a rail as a fire barrier at the lower edge of the module instead of massive fire bars, which in turn reduce the rear ventilation. But this would then be visible in the facade and would contradict the visual requirements of many architects. As far as I know, no one has a finished concept that does not increase the overall investment again.
You already mentioned the smooth handling of the projects. That is also the interface that Arconsol wants to occupy. How can this be achieved?
By starting BIPV at a very early stage - ideally already during the design phase - of the entire building project and continuing it throughout the entire construction and life cycle of the building. Arconsol as a consulting service provider occupies precisely these interfaces between architect, planner, builder, industry and craftsmen. The aim is to minimise the effort involved in planning and to avoid expensive mistakes or problems in the subsequent construction work - or even worse in operation.
How should I imagine this?
When the architect is confronted with BIPV in the project, he has to find a solution. The usual route is via various module manufacturers, who then each plan with their own solutions and products. But of these, only one comes into play. The architect has a huge amount of work with the queries and may not even find the best solution.
What alternative do you offer?
Many don't know that there are manufacturers who can produce modules with a length of five metres and more or who offer different printing technologies and film solutions. That's why we start one step before. Based on our experience, we define the aesthetic ideas beforehand, but also the requirements in terms of energy yield and economic efficiency, and plan accordingly in a product-neutral way. Then we go into the tendering process with a finished concept. After all, that is much less work.
Then it comes to detailed planning and construction. What mistakes are often made there and how can you help?
Ultimately, it's a question of interfaces and responsibilities of the individual trades on the building site. That's why Arconsol offers a complete package from concept consultation to site supervision. This pays off for the client. After all, it is usually only small mistakes that happen because the individual trades and suppliers do not work together, but in the end they can be expensive, if only because of the evidence. However, expert advice ensures that, for example, the strings are planned and built to match the shading situation or that inverters are also planned and the right inverters are supplied. Sounds strange, but it has all happened.
So the goal is that in the end a safely functioning solar system forms the facade or the roof cladding?
So the question is, where is the end? It is not the completion of construction or the handover to the client. Here, the operation of the system must also be considered in the planning and construction stages. After all, building owners will be dissatisfied if the system no longer delivers the predicted yields over time because, for example, water remains on the modules and they become contaminated, or modules cannot be replaced, or because system maintenance has not been priced in.
The performance of the solar systems is of course also a component of the profitability calculation. What do you basically have to pay attention to?
Basically, it is a matter of amortisation calculations, i.e. in what period of time does the solar facade recoup the additional costs of photovoltaics. There is a big difference here between the conventional facade type and the solar facade. If a composite thermal insulation system is planned, which is relatively inexpensive but also has its disadvantages, the difference between a rendered and a solar facade is quite large. In the case of a rear-ventilated facade, which is already of a higher quality in terms of the system, the difference to the solar facade is not so great. In this case, the substructure is necessary anyway and the difference is only between the conventional and the solar-active elements and the additional expense for the electrical installation.
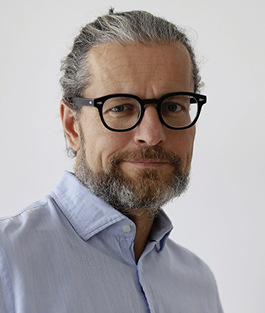
Dieter Moor/Arconsol
The interview was conducted by Sven Ullrich.
In conversation:
Dieter Moor is managing director of the BIPV consultancy Arconsol. Previously, he worked for more than 15 years at Ertex Solar, a module manufacturer specialising in custom-made products. Here he implemented around 2,000 BIPV projects.